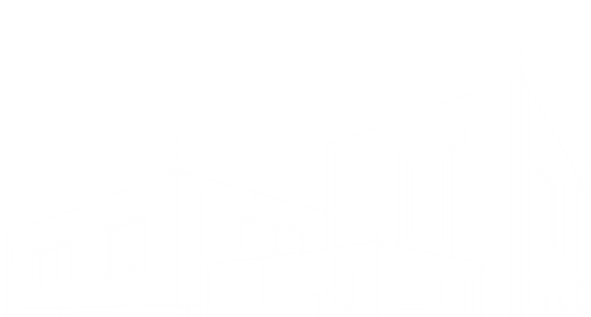
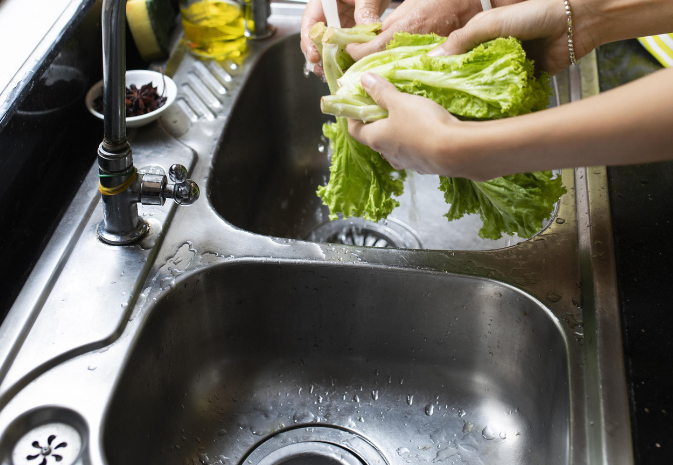
Core Technologies in Stainless Steel Sink Manufacturing
beauty, and easy cleaning. However, high-quality stainless steel sinks are not simply stamped and formed.
The manufacturing process involves a number of core technologies that directly affect the product's service life and user experience.
We will explore the core technologies of stainless steel sink manufacturing factories in depth to help consumers and industry
professionals understand the key production processes of high-quality sinks.
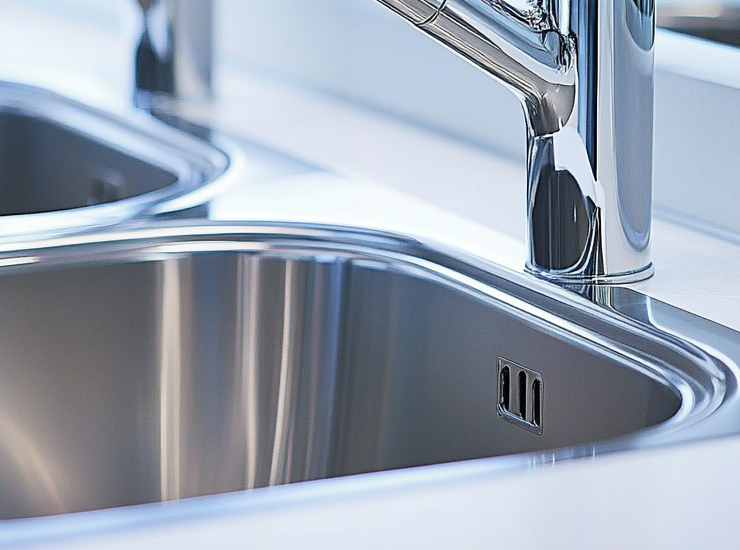
01: Selection of High-Quality Stainless Steel Material
Material Testing: Spectrometer analysis ensures steel composition meets standards.
Surface Finishing: Processes like brushed, mirror polishing, or sandblasting enhance aesthetics and scratch resistance.
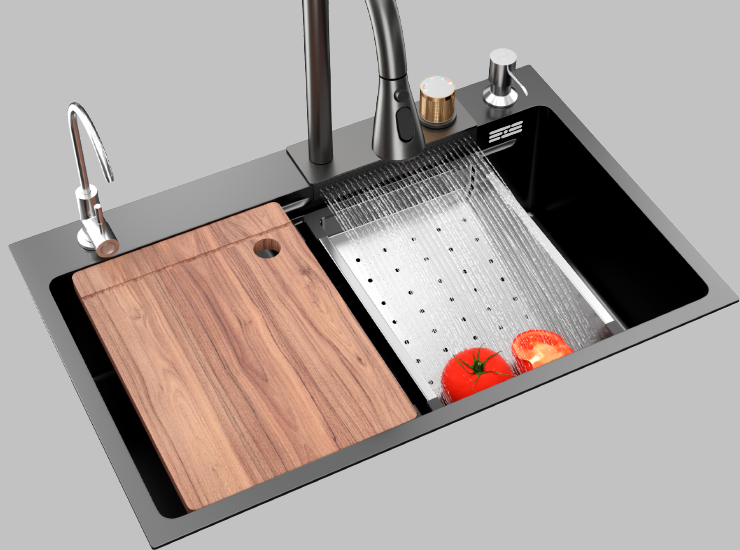
02: Precision Stamping and Deep Drawing Technology
Uses high-tonnage hydraulic presses (500-1000 tons) to stretch a single steel sheet into a seamless sink.
Advantages: No welded seams, preventing dirt buildup; high impact resistance.
Disadvantages: Higher mold costs, typically used for mid-to-high-end products.
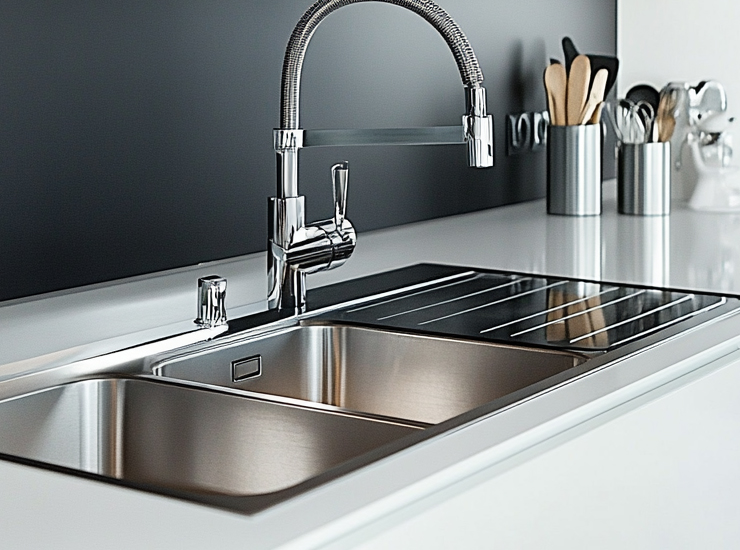
03: Surface Treatment and Anti-Fingerprint Technology
Nano Coating: A hydrophobic and oleophobic layer repels stains.
PVD (Physical Vapor Deposition) Coating: Increases surface hardness, improves scratch resistance, and offers color options (e.g., black, gunmetal).
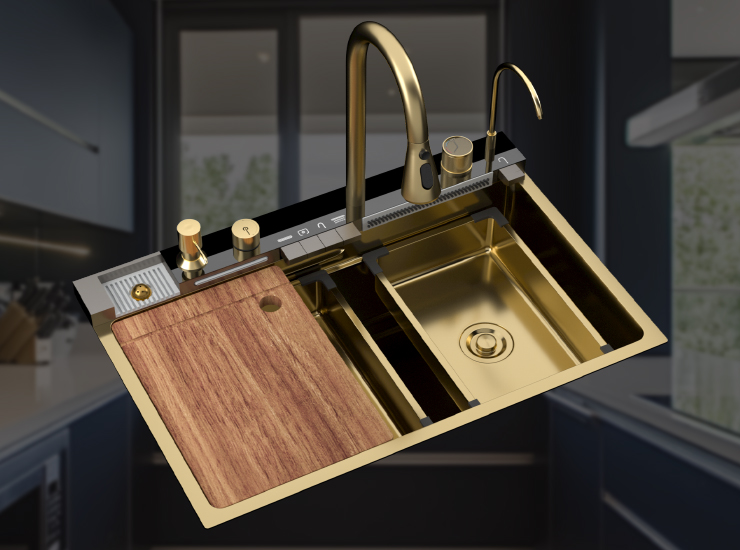
04: Edge Treatment and Leak-Proof Design
Rounded Corners: Smooth edges prevent dirt accumulation and improve safety.
Drip-Free Design: Some sinks feature a water diversion groove to minimize splashing.
Sealing Technology: Silicone gaskets + waterproof adhesive ensure a tight fit with countertops.